Sttr
Crew Member
So I put the stringer installation on hold to put some thought into the new plan. The resin coat is still not sticking to the spruce confirming everyone’s concerns about the quality of the wood. On a positive note I do have a awesome template for the stringers LoL.
Did a bit of prep work for the deck today. Made sure everything is straight and propped up some ply, fit into place, and ended with a coat of resin. The bow will be put together from 3 main pieces and beefed up upfront
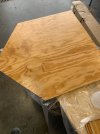
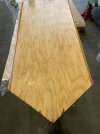
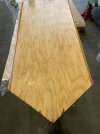
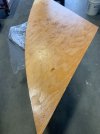
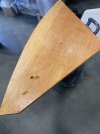
Did a bit of prep work for the deck today. Made sure everything is straight and propped up some ply, fit into place, and ended with a coat of resin. The bow will be put together from 3 main pieces and beefed up upfront
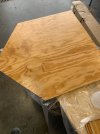
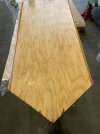
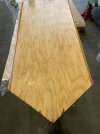
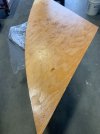
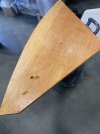