Matthias
Well-Known Member
I'm looking to have a minor glass project done to the transom of my boat and am trying to gauge if a quote from my glass guy is realistic.
The situation is: my kicker bracket is mounted to my swimgrid. There is a support arm connecting the swim grid (right under the kicker) to the transom (only 2 screws). Last year while bouncing around offshore, one screw stripped loose and water got in through the hole. I had it patched but it's not a long term solution. I can't bolt it because there is no access to the other side. The true root cause is the design of the kicker bracket - the transom should bear most of the weight rather than the swimgrid, but beefing up the transom and redesigning the bracket will be out of budget for me.
The plan is to seal the screw hole (pictured), glass a block of wood over top to the transom, and fasten the bracket to the this block so that even if the screws do strip, water isn't getting into the boat.
A guy quoted me 10hrs for the glass work. I have limited glassing experience but my immediate reaction was that was high. It's a small project and I can probably get away without doing anything. I just want to make sure I'm not underestimating that time that into something like this
Any help appreciated!
d!
The situation is: my kicker bracket is mounted to my swimgrid. There is a support arm connecting the swim grid (right under the kicker) to the transom (only 2 screws). Last year while bouncing around offshore, one screw stripped loose and water got in through the hole. I had it patched but it's not a long term solution. I can't bolt it because there is no access to the other side. The true root cause is the design of the kicker bracket - the transom should bear most of the weight rather than the swimgrid, but beefing up the transom and redesigning the bracket will be out of budget for me.
The plan is to seal the screw hole (pictured), glass a block of wood over top to the transom, and fasten the bracket to the this block so that even if the screws do strip, water isn't getting into the boat.
A guy quoted me 10hrs for the glass work. I have limited glassing experience but my immediate reaction was that was high. It's a small project and I can probably get away without doing anything. I just want to make sure I'm not underestimating that time that into something like this
Any help appreciated!
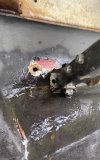