ABYC Standards for seacocks and thru-hulls
Think of it like this: The only thing standing between your safety on a seaworthy dry-bilged boat, and a disastrous 50-gal/89-l-per-minute leak through a 1″/25.4mm through-hull, is a properly installed and secure seacock.
Since each seacock is vital to a boat’s watertight integrity, by selecting the valve and its connectors and components based solely on expense, ease of installation, or because “that’s the way we’ve always done it,” you will put the boat at unnecessary risk. Indeed, if you choose the incorrect seacock materials, they will be impossible to properly install for a given application.
The guidelines set forth in the American Boat & Yacht Council’s Standards and Technical Information Reports for Small Craft, Standard,
H-27: Through-Hull Fittings and Drain Plugs, revised in July 2008, make it clear that seacock installations must be robust and durable. It specifies that each penetration below the waterline should be fitted with a through-hull and a seacock valve. In this context, “below the waterline” means any fitting that is submerged when the vessel heels 7° for powerboats; and to the level of the sheer amidships on sailboats.
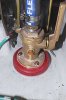
A single exception is detailed below. While the standard is important and a quick read, a few passages are particularly relevant and potentially tricky for builders and repair yards:
•
27.5.1 “All piping, tubing or hose lines penetrating the hull below the maximum heeled waterline, shall be equipped with a seacock to stop the admission of water in the event of failure of pipes, tubing or hose. (Exception 2) Hull penetrations that discharge above the waterline in its static floating position and below the maximum heeled waterline and meet requirements H-27.5.3.”
Therefore, some above-the-static-waterline through-hull fittings might comply while not using a valve per se.
•
27.5.3 “Hull penetrations that are not equipped with a seacock[remember, these may only be above the static waterline—D’Antonio] shall use reinforced piping or hose that resists kinking or collapse.”
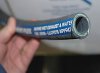
If you opt to forgo the seacock on any fitting above the static waterline, the hose must be reinforced. While “reinforced” is not defined in the standard, to me it means a heavy-walled hose such as one designed for marine wet exhaust and carrying the J2006R designation. Wire-reinforced wet-exhaust hose—a common designation for durable raw-water hoses—would also meet the criteria, although I wouldn’t consider the wire a prerequisite unless the installation risked kinking. My preference is to avoid installing a through-hull fitting within less than 12″ (304 mm) of the static waterline without a seacock, power or sail—regardless of whether the region is submerged during a 7° heel or when heeled down to the sheer amidships. (The term static floating position is defined in detail in the standard, and should be well understood by those carrying out this work.)
•
27.5.4 “Seacocks shall be designed and constructed to meet ANSI/UL 1121, Marine Through-Hull Fittings and Sea-Valves.”
This does not say that just any UL rating or labeling ensures compliance. Valves can be UL listed for countless applications—fuel, LP gas, potable water, and even seawater. Only a few are designated as “sea valves.” Typically, UL-listed sea valves include a flange, although it’s not specified in the standard.
•
27.6.1 The seacock must be able to withstand “a 500 pound static force applied for 30 seconds to the inboard end the assembly, without the assembly failing to stop the ingress of water.”
This means the more hard plumbing directly attached to the seacock, the greater its vulnerability to failure during that test and in service. I recommend a pipe-to-hose adapter, straight or 90°, as the only fitting that should be directly attached to a seacock. A length of hose should separate any additional hard plumbing fittings from the seacock to isolate it from a lever-arm effect. My personal standard is: any raw-water plumbing must pass “the stand-on-it test.” Meaning, if a raw-water plumbing hose, fitting, or fixture is too fragile to be stepped upon without failing or leaking, it’s either too fragile, period; or not well enough protected.
•
27.6.1.2 “Threads used in seacock installations shall be compatible (e.g., NPT to NPT, NPS to NPS).”
This entry, which specifically prohibits the mixing of incompatible thread types, was added to the standard in 2008. While it’s inconceivable to me that any experienced boat builder or mechanic would knowingly attach plumbing components whose threads were incompatible, it’s an all-too-frequent occurrence; thus the specific prohibition.
Hardware throughout the raw-water system should be fully compatible with exposure to seawater. Usually this means bronze (brass should never be installed, because of its zinc content); however, proprietary glass-reinforced plastics such as Marelon are also well suited to seacock and raw-water applications. Avoid PVC; its tensile strength is not high enough to rely on to keep a vessel afloat. Also, conventional 300-series stainless steel is not ideal because of its propensity for crevice corrosion.
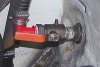
Here is a through-hull fitting attached to an inline ball valve—two components that were never designed to be attached to each other. They do not constitute a proper seacock, and are not compliant with ABYC standards. Because the ball valve’s threads are tapered, and the through-hull’s are straight, they do not properly interface, and make a weak joint at best. Moreover, seacocks are typically flanged to provide adequate load distribution, and on FRP vessels, they often rest on encapsulated marine plywood, GPO 3, or some other suitable composite material backing block. (Never install solid wood of any species for this application.) If the seacock flange includes mounting holes, it must be through-bolted or lagged into the backing block with bronze, not stainless, fasteners.
BTW: I really like having the washdown - keeps blood and guts off the deck while fishing and easy boat clean-up later.