sasqman
Crew Member
Hi all,
Now that I'm looking at a repower with a new motor I need to get my custom bracket rated for horsepower to keep the warranty people happy. Anyone know any structural marine engineers that would sign off on it. I will have the boat out of the water next week to get more accurate measurements.
Here is a pic. Its on the boat right now holding my 115hp merc and preforming well. It did get powder coated before installation as well.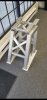
Thanks!
Now that I'm looking at a repower with a new motor I need to get my custom bracket rated for horsepower to keep the warranty people happy. Anyone know any structural marine engineers that would sign off on it. I will have the boat out of the water next week to get more accurate measurements.
Here is a pic. Its on the boat right now holding my 115hp merc and preforming well. It did get powder coated before installation as well.
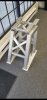
Thanks!
Last edited: